Over the past 2 years we have massively invested in our equipment which included 2 new purpose built Hammlemann ultra high pressure pumps which we hoped would; reduce our impact on the environment, increase our efficiency and improve our operations. We are pleased to report that both pumps have been invaluable to Hydroblast and our clients so much so we have found the need for another new machine. This being a ultra high pressure pump with additional water flow to make certain applications much more efficient.
Need for higher flow
It is vitally important for us to a consider a pump’s flow rate, not just the pressure, when choosing which of our fleet is most suitable for any particular job, as this will have a great impact on productivity and efficiency. This is achieved by having a large volume of water that is directed towards the concrete surface in order to rapidly and continuously pressurise the areas being treated.
Water is a precious resource and without it we couldn’t do our job, therefore we are actively trying to cut our usage when operating our ultra high-pressure pumps wherever and whenever we can. It may seem self-destructive to this that we would prefer higher flow rates for certain jobs, however this may mean that the length of time that the job will take is drastically reduced, therefore saving water in the long run. This is especially key in hydro-demolition and refractory removal.
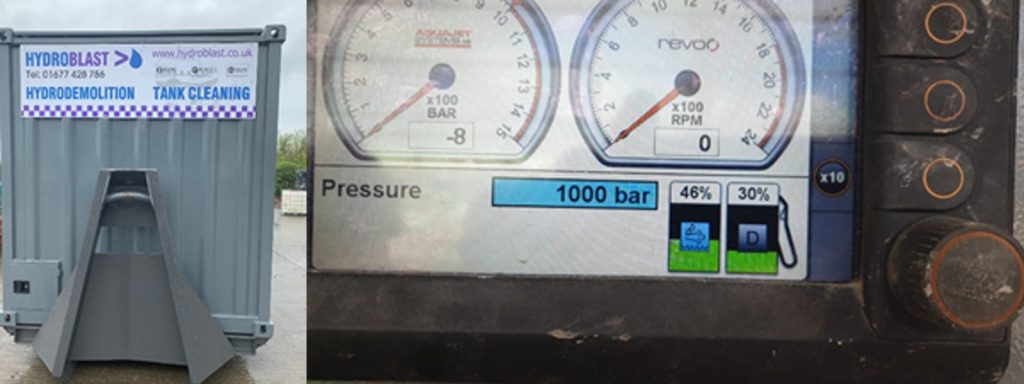
Customer requirements vary each time and there can be vastly different strengths of concrete or refractory. With the added strength that requires a break out sometimes the same as shallower/softer material, this is why it is important to have a diverse range of waterjet equipment. The duration the material is exposed of the water jet will determine the depth of the removal also, which if doing robotically can include; cradle speed, oscillation speed and number traverses.
Another UK first for Hydroblast
During a recent business trip overseas our Director Ross McDonald made connections with a gentleman from France (Olivier Dupont, THP) who are in the same Hydrodemolition industry and operate Hammlemann trailer mounted pumps, as well as UHP, high volume pump. This new PowerPack was exactly what we needed, again filling another gap in our range for pressure and flow, however this would be another massive investment for the business. Ross had the idea to convert one of the powerpacks Hydroblast operate which we already own the same way we previously converted a High pressure (HP) trailer into a UHP pump, just on a much larger scale.
We decided to further invest into the company by purchasing a 503 series Hammlemann 2200 bar pump, which is capable of producing 122 litres per minute. This requires a large engine and is driven off a latest spec Volvo penta (tier 4 stage 2 final) that develops 700 horse power (500kw), that is housed in one of our containers.
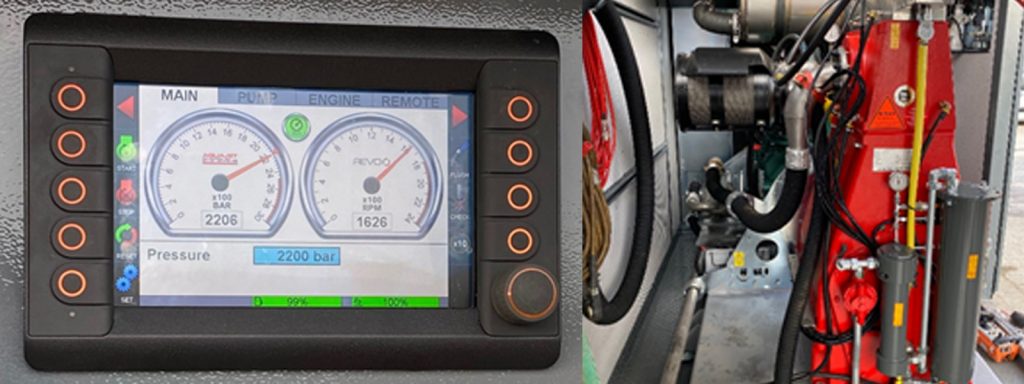
Before this conversion we were running both powerpacks at 1000 and 1040 bar, 262 litres per minute, this demands 15m3 of water an hour. As mentioned, although a large consumption of water, ultimately it uses less water throughout the application as it can be done much quicker. If we can get the same output or better using half the volume , 7m3 an hour then this is a unique selling point we have over our competition.
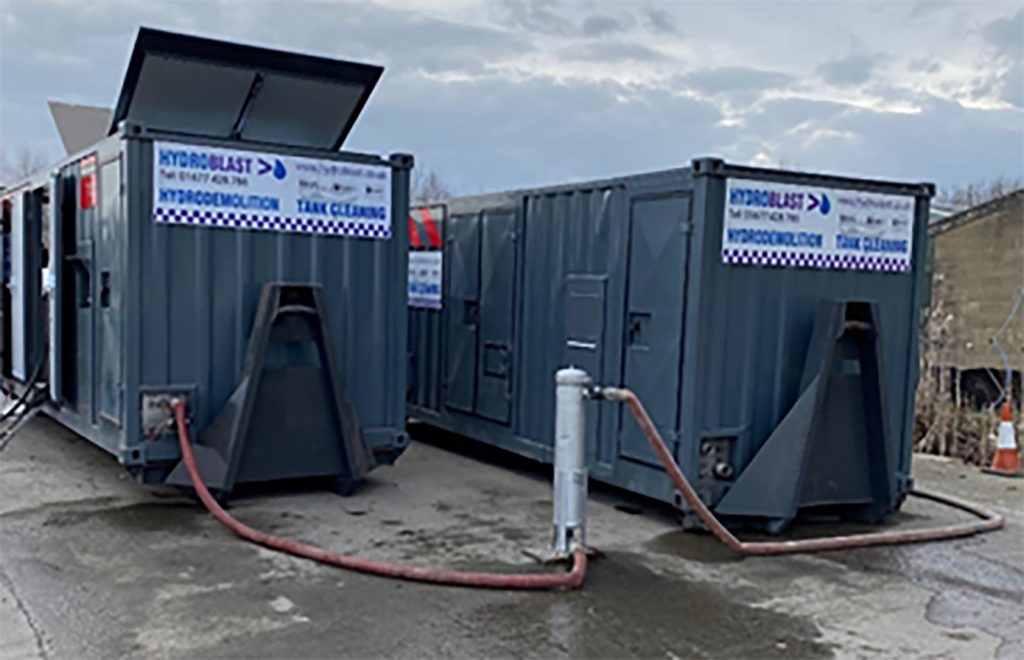
Ultra High Pressure Pump
Its important as part of our commitment to the environment (with our ISO 14001 standard) we continuously look for ways that are more economic. Likewise, some sites don’t always have access to large volumes of water easily and it adds high costs if water has to be transported in.
Our recent conversion was on our Hammlemann Aqua 20, that we have also invested in within the last couple of years. We have converted it from 1400 bar, 78 lpm (used for tank cleaning as well as Hydrodemolition) to 2800, 40 litres per minute that was scheduled for a Robotic paint strip job. Due to the current climate, this operation has been temporarily suspended and will resume later in the year.
This second conversion was again the first of it’s kind in the UK. We are delighted to announce that the conversion work which was carried out within the last fortnight resulted in a successful test. Our ‘new’ PowerPack was due out on its first job in the next few weeks but has been proposed until normality has resumed. We aim to report how it compared to the first visit using 1000 bar soon.
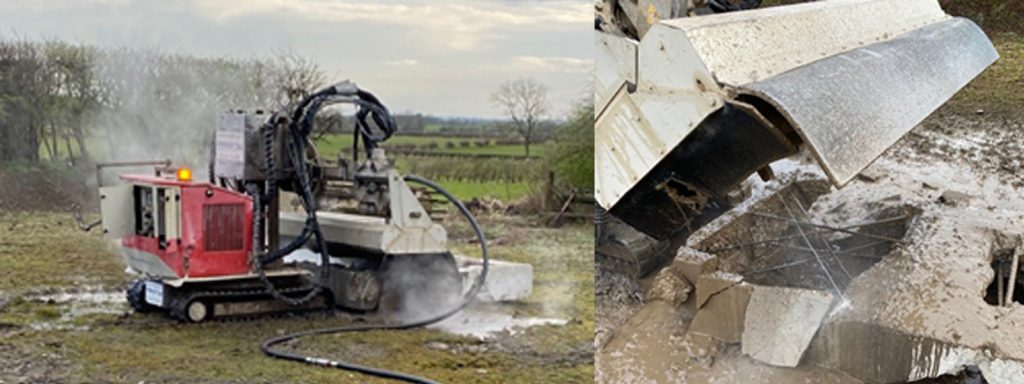
This conversion has the benefit of giving us the flexibility of being able to convert it back again depending on our current workload demand, making it effectively a 4 in 1 UHP Pump. This not only saves us cost which we don’t need to then pass onto our customers but is also much better for the environment than buying a new machine.
If you would like to know more, please contact Hydroblast sales@hydro02.ts3.testdigital.net