The water jetting work took place in Yorkshire. Local to Hydroblast which was a welcome contrast to recent international projects. The job involved various planning and consultancy meetings. This allowed us to work thoroughly and on time. Due to the busy environment where the works took place.
The pipe was over 250m, with no cleaning taking place in the last 30 years.
The main goal of the project was to remove scale build up. We fully flushed the pipe. This was needed before recommissioning.
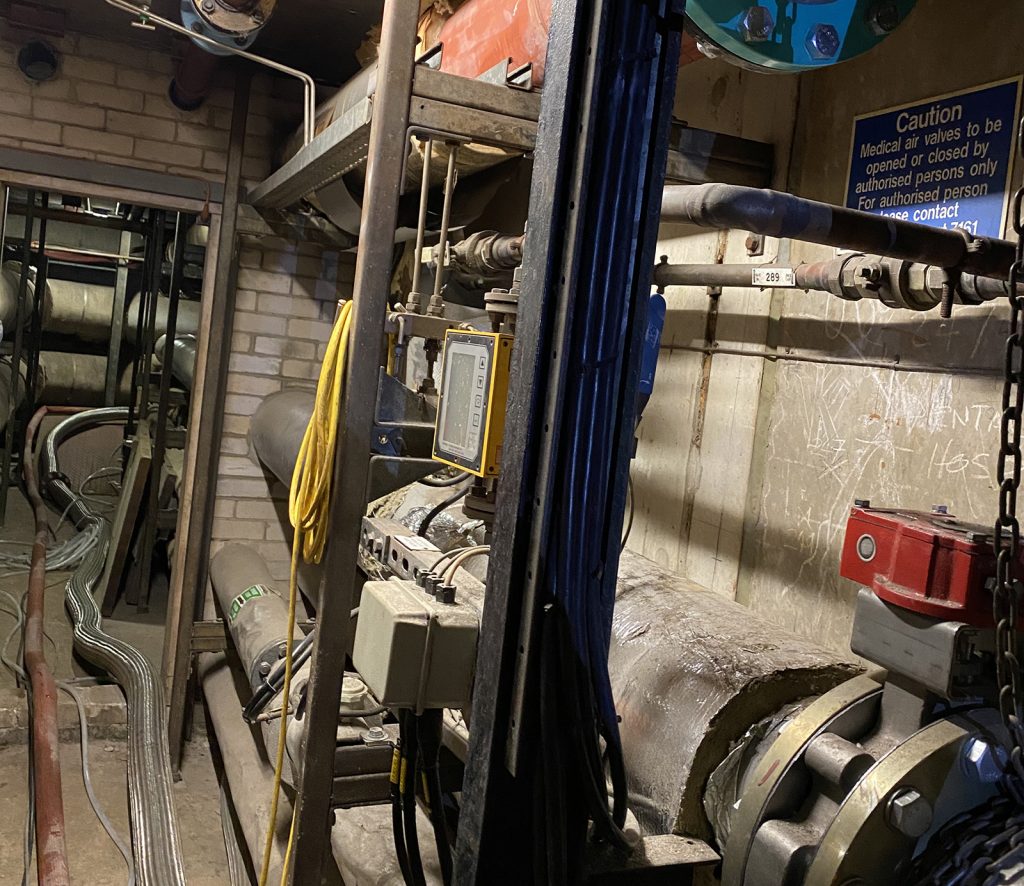
Water Jetting Method
One of our newest Hammelmann pumps was key to the completion of this project. The pump in question was a Aqua 20 capable of pressures up to 1400 bar and 78LPM. An even clean was completed using a 6 inch rotary nozzle with a centraliser. This combination of high pressure was ideal. The pipework needed volume to flush the pipework clean.
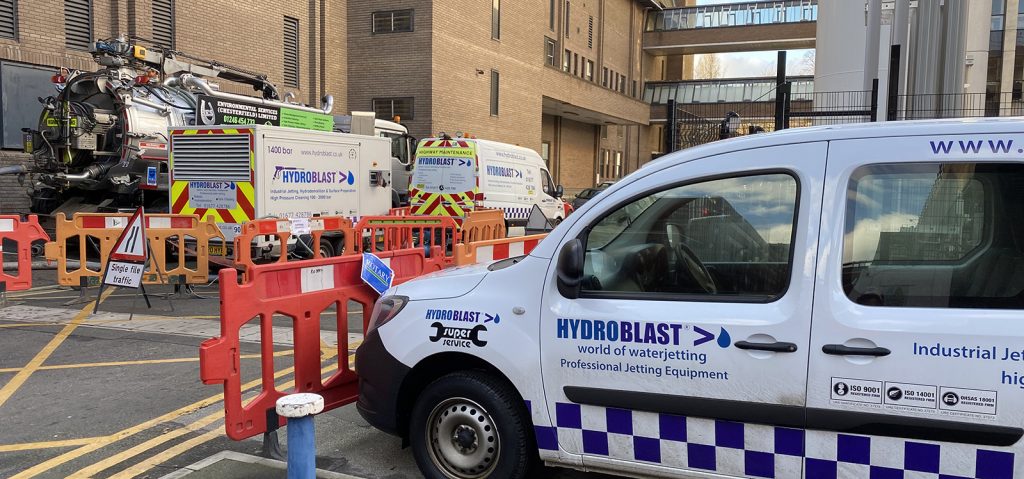
The machine is also very quiet as it is designed to run in a sound dampened box, meaning db levels are lower than other jetting pumps and was ideal for the environment we were working in. Its comfortably also one of the leading manufacturers in the industry. All this aids in the companies ISO 14001 Environmental standards.
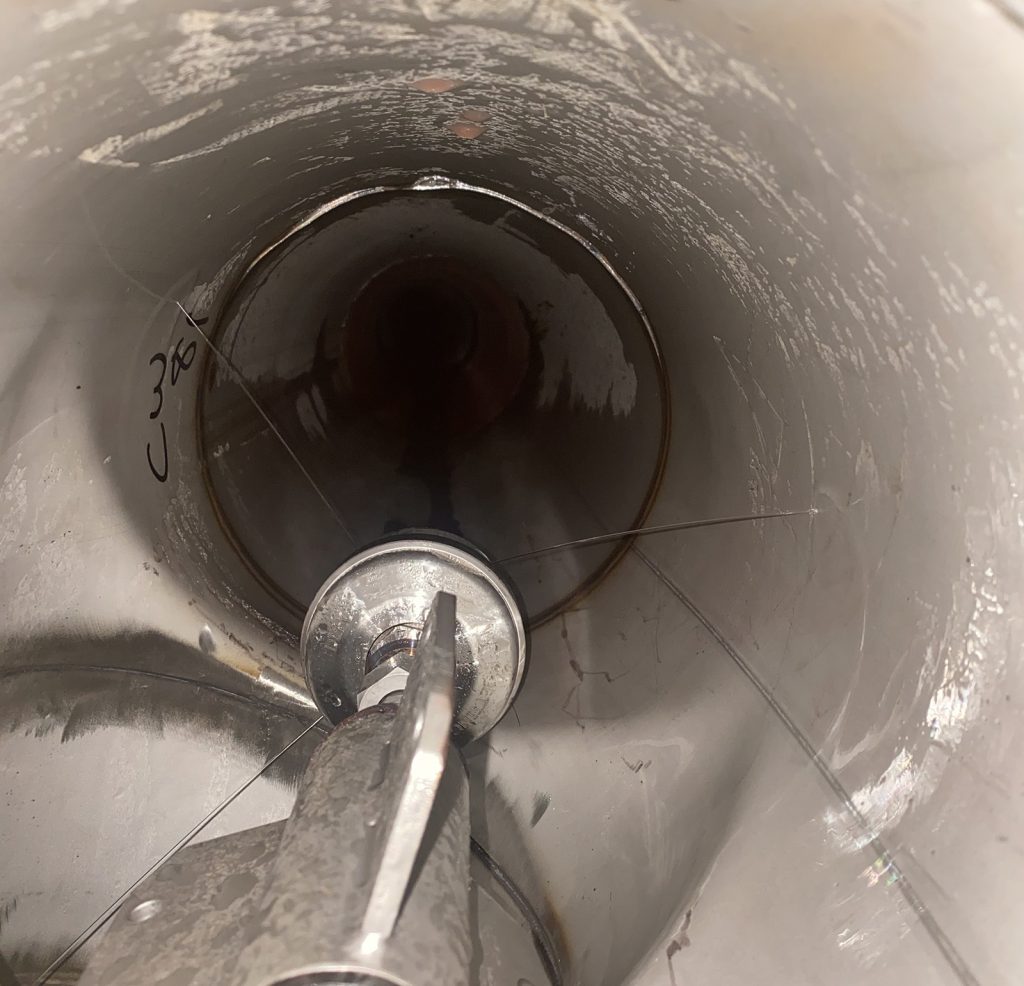
Water Jetting Safety
Safety is always our top priority, and is part of the companies ISO 45001 operating procedures. Clear barriers and signage was visible throughout the project on ground level. Our methodology involved using 2 different types of safety hose. Alongside back out prevention to protect the operator.
Being members of the water jetting association, this is really important for contractors to demonstrate high levels of competency and knowledge using the equipment available in the market.
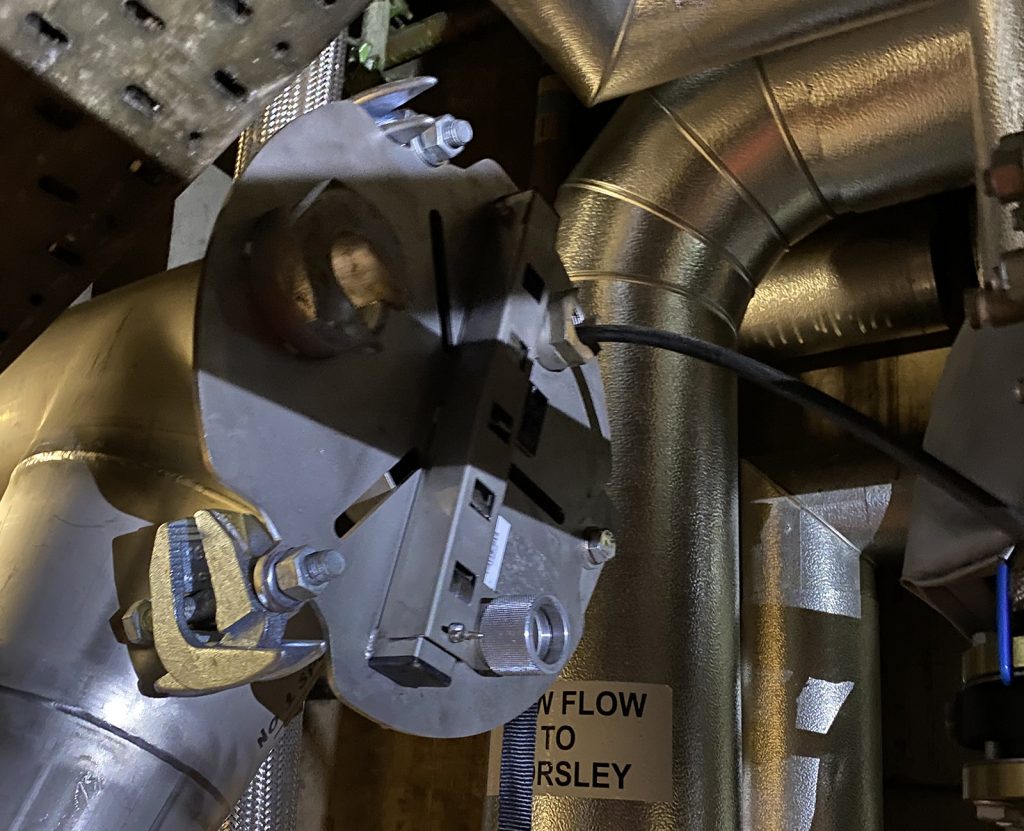
Automated equipment was readily available to hand in case the pipe hose required extra thrust inside the pipe. However, this was not required to the nozzle calculation which gave a steady speed. All of this was managed by the operator.
All of our operators are provided with their own TST suit or Turtle Skin Kevlar clothing. This is worn as part of best practice PPE.
Some may argue this is not necessary due to the existing control measures.
Yes, Water jetting PPE is the last line of defence, it’s the last control measure the company uses , and enforces best practice where possible.
Operations Director Ross McDonald commented:
“Yes the PPE is highly expensive, but you cannot put a cost on an operators health and well-being if there are further measures the company can take where possible. I believe it should be a mandatory requirement for this application. A lot of companies use prevention methods along with automation. It is Unfortunate the methods we employ are not common practise in the industry. this is due to the associated costs. Our aim is to Set the highest standards where possible and ensure everyone completes the work safely. Our Customers are able to see what value we bring and don’t just look at the overall cost”.
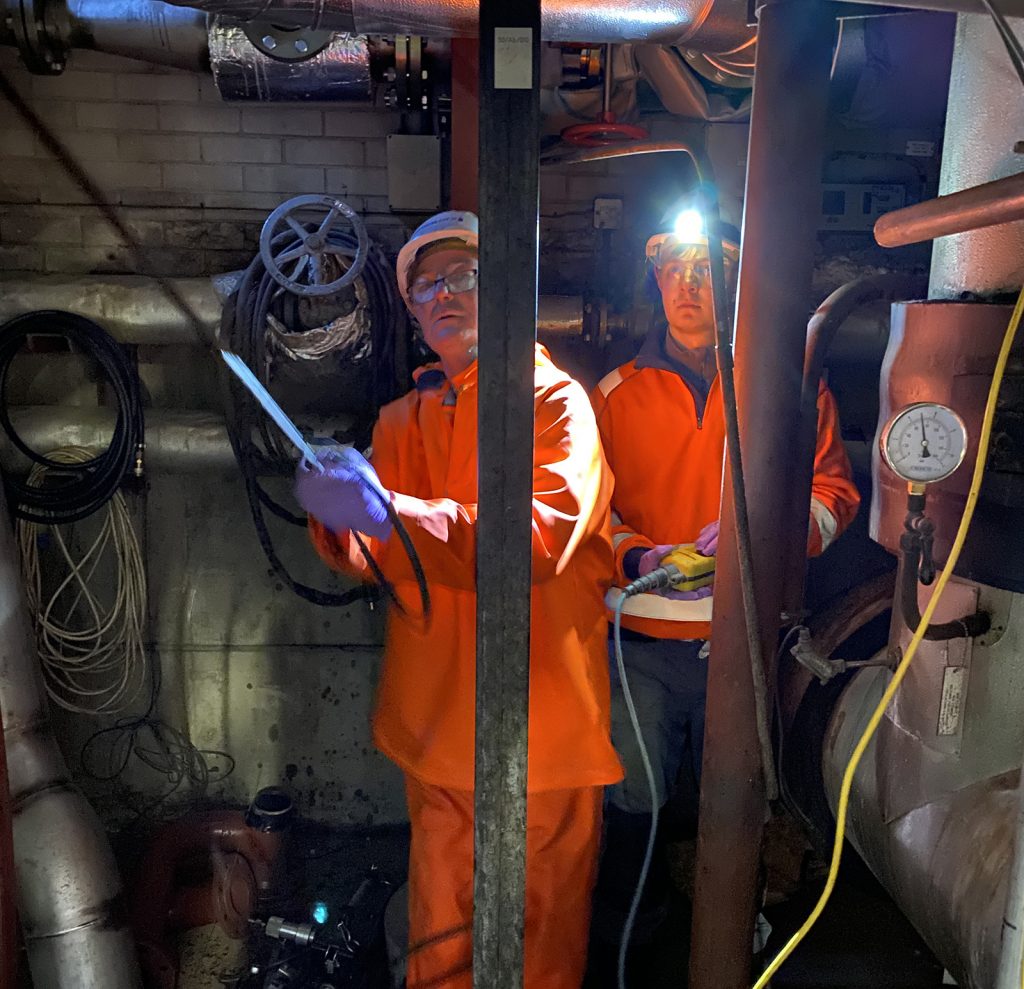
The pump operator watches closely and can shut the machine down using the remote control cable in the event of an emergency.
They had direct contact via radio to the pump man who could monitor the machine , ensure no pedestrians entered the exclusion zone, and could safety turn the unit off when needed.
Another very important aspect of the project was to manage waste water. A liquid ring vac tanker was used to this along with bespoke fixings. As a result the water was collected successfully and disposed of correctly.
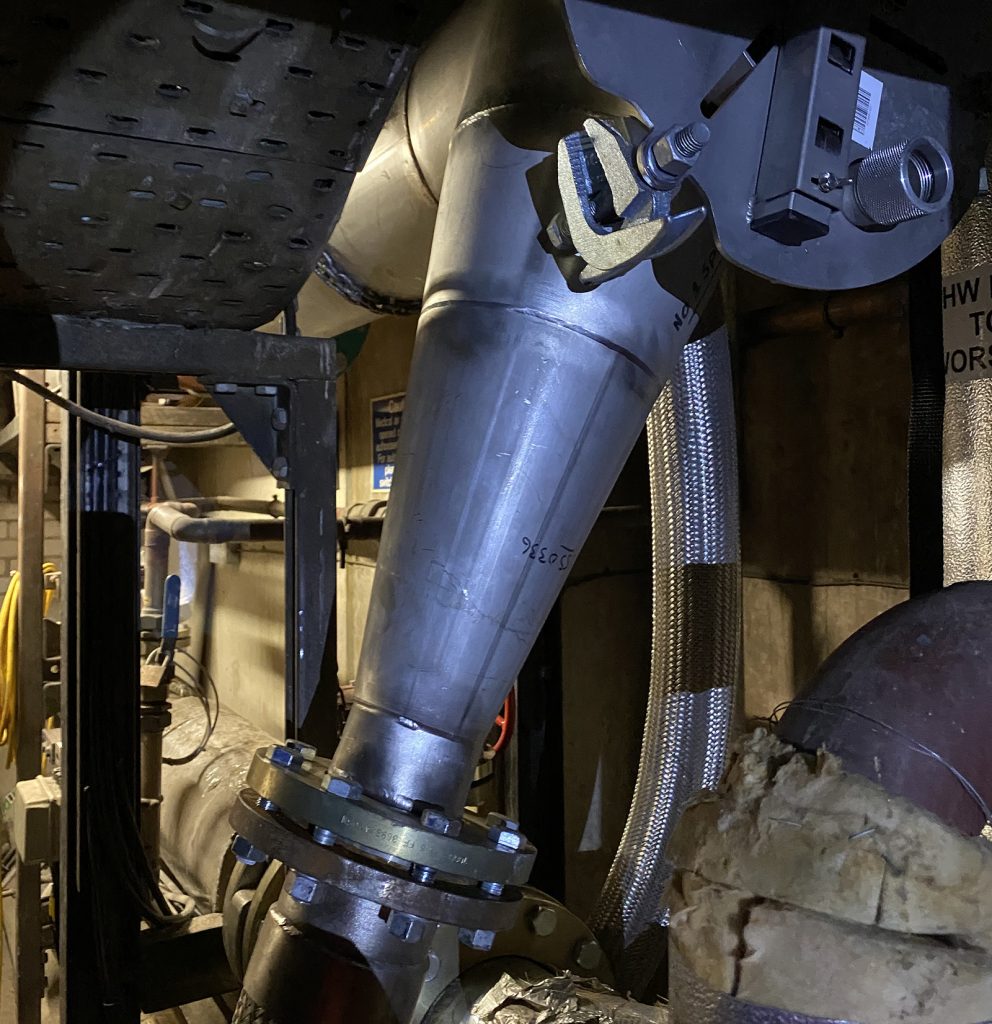
The Results of Water Jetting
We completed the job within 3 days (on time). Due to careful planning by Hydroblast and liaising with the client (who were also helpful throughout and we would like to thank them for that).
The pipe is now back in commission, and we are now on our next water jetting project in South Yorkshire.
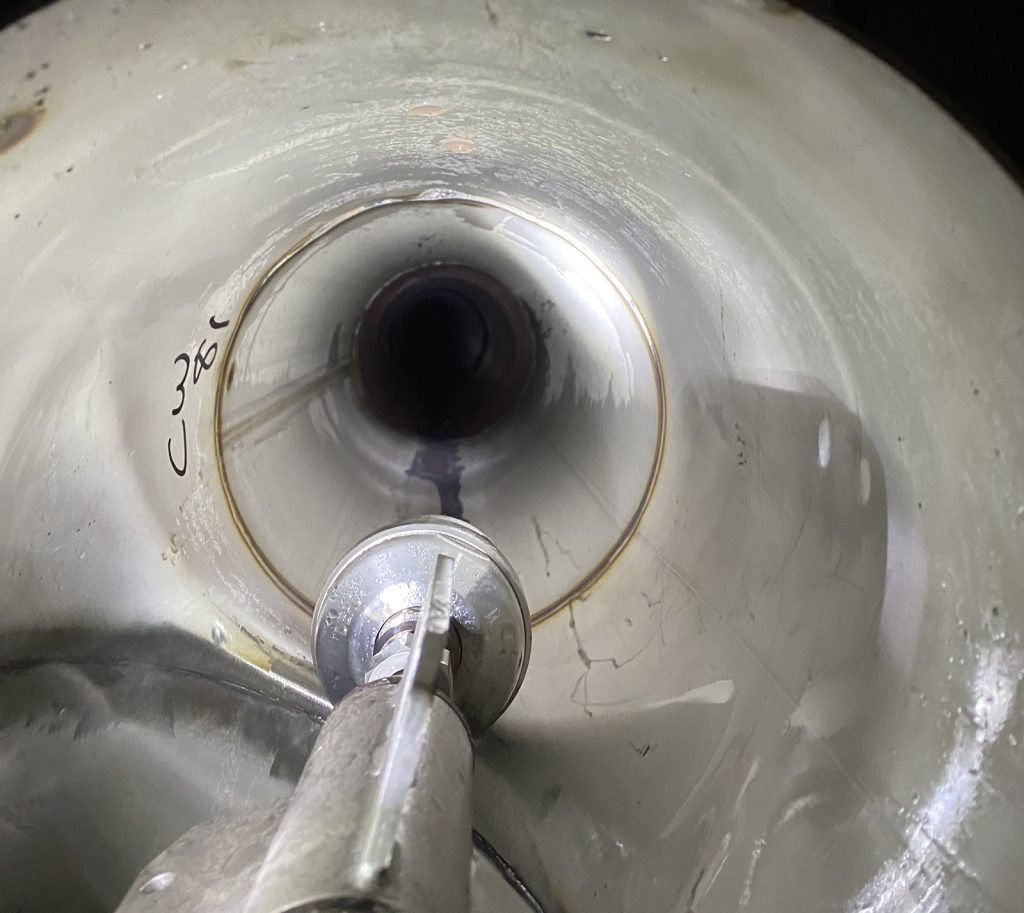